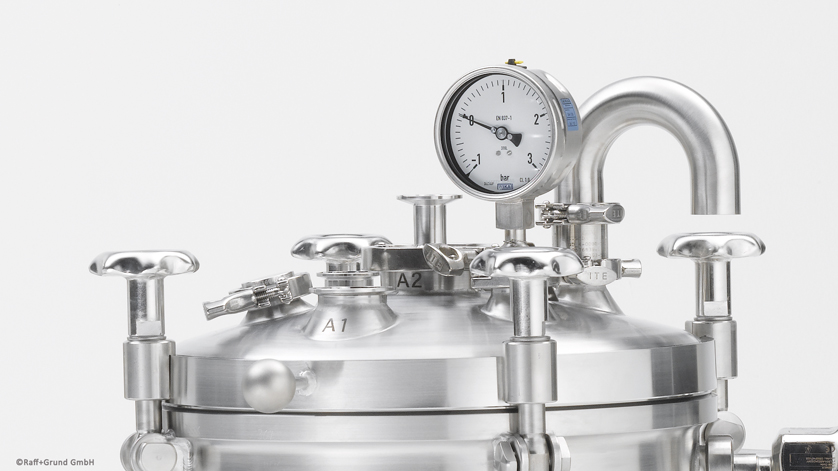
Pressure monitoring in mobile tanks is an important measuring task in the pharmaceutical industry. Among other things, it enables users to check whether the containers are leak-tight during transport. In the case of active ingredients, this is an absolute necessity.
Active pharmaceutical ingredients are high-value products. Pharmaceutical companies therefore do everything they can to avoid any losses. This also applies to the route between the various manufacturing stations of such “active pharmaceutical ingredients” (APIs) and their subsequent further processing. Transport is carried out using mobile tanks. To protect the valuable contents, the remaining empty space in the containers is blanketed with inert gas.
Falling pressure in the mobile tank is an indication of a leak
Pressure monitoring for mobile tanks during transport extends to this zone. The pressure in it must be constant. However, if the pressure falls, this is an indication of a leak in, for example, a valve or a seal. Active ingredients can either escape or become contaminated through this leakage. If the corresponding pressure is indicated, users can react immediately to prevent major economic damage or to prevent a possible danger to the environment due to escaping medium.
Which instrumentation is recommended for pressure monitoring in mobile tanks? Pressure gauges are usually used for this task. They work purely mechanically and do not require any external energy to measure and indicate pressure. The user, therefore, always receives a reliable measured value. However, the instruments must be designed to meet the task.
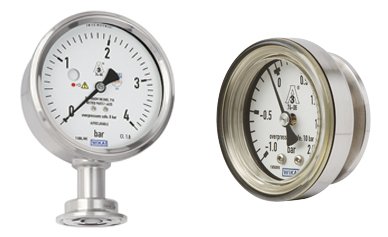
The model PG43SA-D (left) and PG43SA-C diaphragm pressure gauges have a hygienic design and are also autoclavable.
Diaphragm pressure gauges for a wide range of applications and high safety requirements
A wide range of applications can be covered with two diaphragm pressure gauges from WIKA’s PG43SA series. The general advantage of diaphragm pressure gauges, in addition to the high overload safety, is the “dry” operation of the measuring cell, which poses no risk of contamination for the medium. In addition, the PG43SA instruments have a hygienic design with a diaphragm element welded flush to the front. They are suitable for CIP/SIP cleaning processes and are also autoclavable.
Integrated diaphragm element monitoring
WIKA has developed the model PG43SA-D for particularly high safety requirements. The instrument has an additional integrated diaphragm element monitor with red/white indicator. Should the otherwise robust measuring element tear as a result of a particularly aggressive medium, the user immediately receives an indication (red) of the damage. A second barrier in the instrument keeps the pressure gauge sealed until the damage has been repaired.
The model PG43SA-C is suitable for small tanks with a capacity of up to 20 litres. With this compact instrument, the process connection is integrated into the case to save space. Due to the patented design, the pressure gauge is also suitable for containers from which no instrumentation may protrude due to the risk of it being torn off.
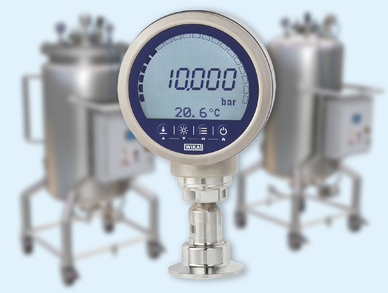
The model CPG1500 precision digital pressure gauge with fitted hygienic diaphragm seal is recommended due to its high accuracy and a powerful data logger.
Highly accurate pressure monitoring for mobile tanks with complete documentation
However, if the focus of the measuring task is on accuracy and/or there is a need for documentation for transport, a diaphragm seal system with the model CPG1500 precision digital pressure gauge and a hygienic process connection is the first choice.
The pressure gauge measures with an accuracy of up to 0.1 percent of span. It also has a high-performance data logger that enables complete information about the pressure profile. The information can also be read out via Bluetooth® and archived for later review by the responsible authorities.
Vibration and shock-resistant
The mechanical design of the CPG1500 also enables it to be used in critical applications. It has comparatively few mechanical components and is therefore very resistant to vibration and shock, which is particularly advantageous when transporting by forklift, truck or plane. In applications with highly aggressive ingredients or cleaning agents, the wetted parts of the diaphragm seal fitted to the pressure gauge can also be made of special materials, such as Hastelloy®.
Note
For detailed information about the PG43SA-C and PG43SA-D diaphragm pressure gauges as well as the CPG1500 precision digital pressure gauge , please visit the WIKA website. There you will also find an overview of other measuring solutions for the pharmaceuticals and biotechnology sector as well as the “Sanitary applications” brochure for downloading. If you have any questions, your contact will gladly help you.
Also read our posts
Pharmaceutical industry: Level monitoring using differential pressure
Flexible pressure monitoring in blood plasma processing
Pressure monitoring in the pharmaceutical industry with a universal instrument