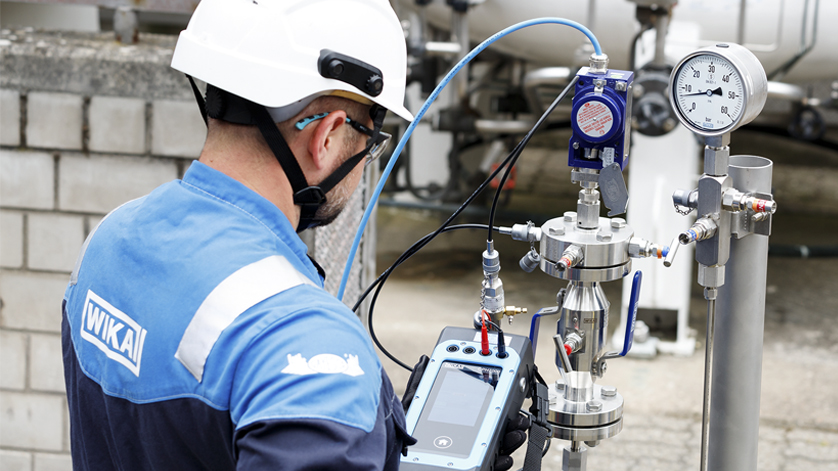
Eine In-situ-Kalibrierung von Messgeräten kommt für zahlreiche Industrieprozesse in Frage. Ihre Vorteile liegen auf der Hand: Die Geräte bleiben installiert, die Prozesse müssen demzufolge nicht geöffnet werden. Die Anlagenbetreiber senken auf diese Weise den Zeit- und Kostenaufwand für die Prüfung. Zugleich schließen sie potenzielle Fehler beim Wiedereinbau der Geräte nach einer Kalibrierung im Labor aus. Voraussetzung für eine In-situ-Kalibrierung ist in der Regel die Einrichtung der Messstelle mit entsprechenden Instrumentierungsventilen, im Folgenden anhand eines Beispiels von Druckschalter-Messstellen in einer Verbrennungsanlage für flüssige Abfälle dargestellt.
Bei dem Betreiber der Anlage handelt es sich um ein Unternehmen, das auf die Entsorgung schadstoffbelasteter Reststoffe aus der chemischen Industrie spezialisiert ist. In dessen Verbrennungsanlage für flüssige Abfälle übernehmen 46 Druckschalter zentrale Überwachungsaufgaben. Hierbei geht es in erster Linie um die Aufrechterhaltung der Energieversorgung für den Verbrennungsprozess. Sollte der dafür notwendige Druck unter den definierten Grenzwert sinken, lösen die Messgeräte einen Verfahrensstopp aus. Denn bei unzureichender Versorgung mit beispielsweise Erdgas, Luft und Dampf kann die Anlage die eingespeisten Substanzen nicht fachgerecht verbrennen. Der Betreiber muss also in einem solchen Fall umgehend die Ursache für den unzureichenden Druck ermitteln. Eine verstopfte Leitung oder ein technischer Defekt wären typische Beispiele.
46 Druckschalter verursachen einen beträchtlichen Prüfaufwand
Die Kalibrierung der Druckschalter erfolgt einmal jährlich während des turnusmäßigen Anlagen-Shutdowns. Bislang ließ das Unternehmen dafür die Geräte ausbauen. Das heißt: Sie wurden erst elektrisch getrennt und dann ausgebaut. Die Druckschalter kamen anschließend ins werkseigene Prüflabor und nach erfolgreicher Kalibrierung und eventueller Justierung zur Montage in die Anlage zurück. Angesichts der Zahl von 46 Druckschaltern verursachte der Prüfprozess einen beträchtlichen Aufwand, zusätzlich verstärkt durch enge Einbauumgebungen.
Das Unternehmen suchte nach einer Alternative und verwirklichte in Zusammenarbeit mit WIKA die Möglichkeit zur In-situ-Kalibrierung. Sie fußt auf zwei Instrumentierungsventil-Typen von WIKA, mit denen die Druckschalter verschraubt und an den Prozess angeschlossen wurden. Je nach Einbausituation handelt es sich dabei um den kompakten Monoflansch Typ IVM und den Ventilblock Typ IV2, beide in Block-and-bleed-Ausführung. Da die fraglichen Messstellen sicherheitsrelevant sind, entschied sich das Unternehmen für Ventilvarianten mit abnehmbarem Griff: Sie verhindern ein ungewolltes Verstellen der Ventile und somit eine Beeinträchtigung oder gar Außerbetriebnahme des angebauten Messgeräts.
In-situ-Kalibrierung erhöht die Anlagenverfügbarkeit
Für die In-situ-Kalibrierung schließt der Bediener zunächst das Block-Ventil. Damit trennt er die Druckversorgung der Schalter vom Prozess. Anschließend folgt die Entlüftung über den Bleed-Port. Dieser ist zugleich die Schnittstelle für den Kalibrator und die Pumpe zur Erzeugung des Prüfdrucks. Mit dem mobilen Prüfgerät wird der Schaltpunkt dreimal angefahren und gegebenenfalls justiert. Die Kalibrierung ist damit in deutlich kürzerer Zeit abgeschlossen, was die Anlagenverfügbarkeit erhöht. Zugleich wird in einem Zug der komplette Loop vom Druckschalter bis in die Leitwarte geprüft. Hierbei erhält der Bediener auch Kenntnis über die Abweichung der gesamten Wirkkette im elektrischen Loop, bis hin zu Anzeige, Alarmierung oder Schaltaktion.
Doch eine Messstelle für In-situ-Kalibrierung bietet noch einen weiteren Vorteil: Bei einem Fehlerverdacht zwischen den regulären Kalibrierintervallen lassen sich die Schaltfunktionen und Grenzwerte einzelner Druckschalter auch bei laufendem Prozess prüfen.
Ventile erfüllen hohe Ansprüche an Sicherheit und Lebensdauer
Die für die In-situ-Kalibrierung ausgewählten Instrumentierungsventile von WIKA entsprechen den Anforderungen des Kunden an Sicherheit und Lebensdauer der Prozesskomponenten. Die Oberteile der Typen IV2 und IVM verfügen über eine ausblassichere Ventilspindel sowie eine nichtrotierende Spindelspitze mit Metallsitz für einen verschleißarmen Betrieb. Ein niedriges Drehmoment gewährleistet eine leichtgängige und präzise Ventileinstellung, selbst bei hohen Drücken. Beide Ventile gibt es auch in einer Ausführung zur Verhinderung flüchtiger Emissionen gemäß ISO 15848-1 und TA-Luft (VDI 2440).
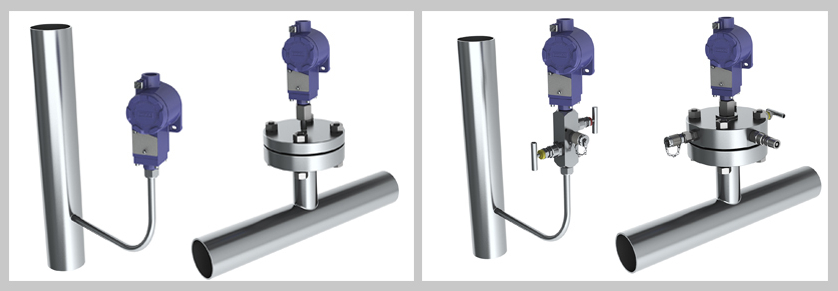
Vorher – nachher: Druckschalter-Messstellen in herkömmlicher Ausführung (linke Abbildung) und mit WIKA-Instrumentierungsventilen für eine In-situ-Kalibrierung (rechte Abbildung), im vorliegenden Fall mit Ventilblock Typ IV2 und Monoflansch Typ IVM (r.).
Hinweis
Auf der WIKA-Webseite finden Sie weitergehende Angaben zu den Instrumentierungsventilen IVM und IV2 sowie einen Überblick über andere Ventile und Schutzvorrichtungen. Darüber hinaus können Sie sich dort über WIKAs messtechnische Lösungen für die Chemieindustrie allgemein und speziell zur Verhinderung von flüchtigen Emissionen informieren. Für das Vor-Ort-Kalibrieren von Druckmessgeräten stellen wir Ihnen auf der Webseite ferner den portablen Prozesskalibrator CPH7000, die Handprüfpumpe CPP30 sowie das Präzisionsdigitalmanometer CPG1500 vor.
WIKA bietet außerdem für alle Ventile einen kundenspezifischen Zusammenbau mit einem Messgerät an. Solche Geräte-Hook-ups werden betriebsbereit und dichtheitsgeprüft ausgeliefert.
Bei Fragen steht Ihnen Ihr Ansprechpartner gern zur Verfügung.
Lesen Sie außerdem unsere Beiträge
Flüchtige Emissionen durch Vorbeugung vermeiden
Mit Double Block & Bleed auf Nummer sicher gehen
Wie funktioniert ein Monoflansch?
Druckmessgeräte-Armaturen-Kombi: Hook-up statt Eigenbau