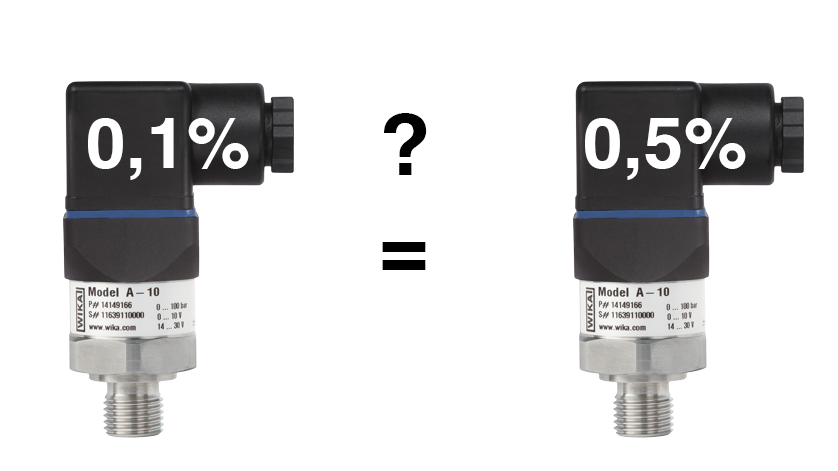
La exactitud tiene su precio: Cuanto más exacta sea la medida, más caros serán los instrumentos de medición. Por otro lado, la falta de exactitud podría resultar aún más caro, en particular si la calidad del producto sufre por ello. Por lo tanto, la exactitud debe ser un factor importante a la hora de elegir un sensor. Sin embargo, solo podrá adoptar la decisión correcta si encuentra el camino apropiado dentro del «laberinto» de los datos sobre la exactitud. En el presente artículo el autor explica los parámetros y criterios más importantes utilizando el ejemplo de un sensor de presión industrial.
El término «exactitud» existe solo en el idioma de los usuarios. No está definido en ninguna norma. Sin embargo, este término aparece en muchas hojas técnicas sobre sensores. Desafortunadamente, no existe ningún concepto común sobre el significado exactitud. No existe «una exactitud», sino una gran cantidad de diferentes especificaciones al respecto. Los factores relevantes para los sensores de presión referente a la exactitud se definen de manera única en todos los estándares. Sin embargo, los datos de los fabricantes difícilmente pueden compararse entre sí, ya que los fabricantes deciden por sí mismos qué información se especifica en la hoja de datos y cómo.
Incluso si dos fabricantes utilizan los mismos términos, no se puede garantizar que ambos signifiquen lo mismo.Con frecuencia, las novedades importantes simplemente se dejan a un lado. Esto significa que: dos instrumentos que tienen la misma «exactitud» pueden diferir considerablemente vistos más de cerca. Lo mismo se aplica en el caso opuesto.
Los siguientes apartados explican los motivos porque dos sensores diferentes, que presumiblemente pertenecen a diferentes clases de exactitud, muestran un valor casi idéntico.
La exactitud de los sensores de presión – Los 3 errores más comunes
No linealidad de un sensor de presión
Para muchos usuarios, la no linealidad es el dato de exactitud más significativo y, por lo tanto, el más utilizado. Sin embargo, la no linealidad a menudo se denomina de manera incorrecta como linealidad. La no linealidad describe hasta qué punto una curva característica está «curvada» o «no es lineal». Indica la mayor desviación posible entre la curva característica y la línea recta ideal.
En general, hay tres métodos para determinar esta línea recta ideal: Ajuste de punto límite, ajuste de valor mínimo (BFSL) y ajuste de origen, siendo este último el menos frecuente.
En el caso de la no linealidad según ajuste del punto límite, la línea recta ideal pasa por el punto inicial y final de la curva; con el método BFSL (Línea recta de mejor ajuste), la línea de referencia se selecciona de manera que la desviación positiva máxima y la desviación negativa máxima sean idénticas. La no linealidad según el ajuste del punto límite proporciona el mayor valor absoluto comparado con el ajuste del valor mínimo, pero es más comprensible para el usuario. La no linealidad según el ajuste del valor mínimo es el valor más significativo en muchos casos porque describe el potencial de la curva característica
El grado real de diferencia entre la no linealidad según el ajuste del punto límite y según el método BFSL depende de la forma típica de la curva característica de un sensor de presión en particular. La no linealidad puede ser el doble de acuerdo con el ajuste del punto límite. Desafortunadamente, muchas hojas técnicas no indican el método que se ha utilizado para determinar la no linealidad. Con frecuencia, los datos solo se pueden comparar tras consultar al fabricante (figura 2).
Valores típicos de un sensor de presión
No hay dos productos idénticos. Esta afirmación también se aplica a la exactitud de los sensores de presión. En realidad, la no linealidad de un número elevado de dispositivos será considerablemente mejor que el valor máximo especificado en la hoja técnica. Solo de esta manera se puede garantizar que la desviación no exceda de un cierto valor máximo debido a tolerancias o variaciones. Esta exactitud (mejorada) se describe como valor típico. Por lo tanto, estas precisiones a menudo se marcan con «tip». (figura 3).
Sin embargo, casi ningún fabricante especifica claramente cuántos dispositivos realmente cumplen con esta «exactitud típica». En general, puede suponer que una «exatitud típica» se corresponde con el valor 1 sigma de la distribución de Gauss, es decir, aproximadamente el 68,27% de los dispositivos cumplen con este valor típico.Si se proporciona una exactitud típica, el usuario sabe que el fabricante no garantiza que el 100% de los dispositivos entregados cumplan con la exactitud dada. Dependiendo de la distribución de los valores medidos, el valor máximo puede ser el doble o el triple del valor típico.Por cierto, los valores típicos se pueden encontrar no solo con la no linealidad sino también con otras especificaciones de exactitud.
Error de medida de un sensor de presión
Probablemente el valor más «fiable» es el error de medida. Puede determinarse sin ningún esfuerzo adicional directamente a partir de la curva característica y contiene todos los errores relevantes a temperatura ambiente, tal como la no linealidad, histéresis, no repetibilidad y error de medición al principio y al final del rango de medida. Si el usuario maneja el dispositivo a temperatura ambiente, este es el error real con el que se mide la presión (figura 4).
El error de medida es la mayor desviación existente entre la curva característica real y la línea recta ideal. La histéresis se define como la desviación máxima de la curva característica en el descenso y el ascenso. La no repetibilidad es la mayor desviación que se obtiene al realizar tres medidas en condiciones idénticas. Desafortunadamente, el fabricante especifica el error de medida en muy raras ocasiones porque, como es comprensible, siempre es mayor que la no linealidad. En general, se proporciona la no linealidad y el error de medición al principio y al final del rango de medición se indica por separado. Los dos últimos en la práctica se denominan error de punto cero y error de intervalo, y el intervalo es la diferencia entre el extremo inferior de la escala y el valor de la escala completa.
Error de temperatura de un sensor de presión
No importa si se usa la no linealidad o el error de medida: Todas estas especificaciones de exactitud describen un sensor de presión a temperatura ambiente. Si la temperatura de trabajo es mayor o menor, también se debe considerar un error de temperatura. El error de temperatura a menudo se indica como coeficiente de temperatura basado en un intervalo de 10 K. El coeficiente de punto cero y el coeficiente de ganancia se indican por separado. Un dispositivo que tenga una exactitud suficiente a temperatura ambiente puede duplicar su error con una desviación de 10 K (figura 5).
Muchos usuarios no saben que tienen que agregar los coeficientes de temperatura del punto cero y el intervalo para calcular el error del valor de escala total. Los errores de temperatura también pueden derivar de desviaciones de la temperatura media o ambiente.
Estabilidad de un sensor de presión
La exactitud indicada en las hojas técnicas generalmente describe la condición de un instrumento al final del proceso de producción. El dispositivo puede estar expuesto a condiciones ambientales que afecten negativamente a su exactitud desde el momento en que abandonan la empresa o el almacén del fabricante o durante el transporte.
No importa cuán exacto sea el instrumento o si es de una calidad muy alta, cada instrumento cambia su exactitud durante su vida útil. Este cambio se denomina deriva a largo plazo o estabilidad a largo plazo. La dimensión de esta deriva viene influida en gran medida por las condiciones de funciona-miento, es decir, las presiones, las temperaturas y otras influencias a las que está expuesto el dispositivo.
En muchos casos, la estabilidad tiene una mayor influencia en la desviación global que, por ejemplo, la no linealidad. Valores dos o tres veces más elevados son frecuentes.Los datos de estabilidad declarados por el fabricante difícilmente pueden compararse. Diferentes estándares describen pruebas muy diferentes para determinar la estabilidad. Además, ninguna de estas pruebas es una copia exacta de las condiciones reales de uso. Esto no es posible porque las condiciones varían mucho de una aplicación a otra. En consecuencia, los datos de estabilidad solo son válidos para su uso en laboratorios o en condiciones de referencia.
Sin embargo, incluso si se utiliza en condiciones de referencia, es casi imposible obtener datos comparables. No puedes hacer que el tiempo vaya más rápido. Y todos los intentos de simular un efecto de lapso de tiempo mediante choques térmicos y otros métodos son solo intentos.
Elementos de la exactitud de presión en la práctica
La histéresis y la no repetibilidad son prácticamente los únicos errores con los que tendrá que convivir. Todos los demás errores pueden minimizarse o incluso eliminarse con algún esfuerzo. Esto funciona con mayor claridad y facilidad utilizando el error de compensación. El usuario puede leer sin problemas el error de compensación en condiciones no presurizadas e introducirlo como compensación en el instrumento de evaluación correspondiente. Para eliminar el error de intervalo, la presión debe regularse exactamente al valor de escala completa.
Esto a menudo no es posible ya que no hay un valor de referencia para la presión. Con el fin de que el sensor de presión no mida peor que antes, la presión de referencia debe ser tres veces más precisa que la exactitud deseada.
La no linealidad solo puede minimizarse con cierto esfuerzo por parte del usuario, por ejemplo, deduciéndola en el sistema electrónico conectado basado en puntos. Incluso en este caso, se requiere un estándar de medida altamente preciso. Sin embargo, estos errores son completamente irrelevantes en algunas aplicaciones y solo resulta importante la no repetibilidad. Si, por ejemplo, la tarea consiste en regular siempre la misma presión, el error se puede compensar fácilmente si se conoce; el resto es la no repetibilidad y la estabilidad a largo plazo.
El error de temperatura se puede estimar fácilmente a temperaturas de trabajo constantes, pero si su aplicación cubre un rango de temperatura más amplio, es mucho más difícil. Desafortunadamente, muchos usuarios aún asumen que los sensores de presión no presentan un error de temperatura adicional dentro del rango nominal de temperaturas. Sin embargo, el rango nominal de temperaturas es solo el rango para el cual los coeficientes de temperatura resultan válidos.
La mayoría de los fabricantes recomiendan calibrar los sensores de presión una vez al año, para controlar si aún cumplen con sus especificaciones. El dispositivo no se reajusta, pero se analiza el cambio real, es decir, la deriva. Si la deriva es más elevada que el valor especificado por el fabricante, podría ser una indicación de que estamos utilizando un dispositivo defectuoso. Cuanto mayor sea la inestabilidad, mayor será la probabilidad de que el sensor esté defectuoso. En este caso, no se puede garantizar la fiabilidad del proceso si el dispositivo todavía se está utilizando. Esta comprobación no requiere mucho esfuerzo. A menudo resulta suficiente verificar si ha cambiado el punto cero del dispositivo sin presión. Si el dispositivo no puede ser comprobado en el sistema ni desmontado para su examen, al menos debe establecer un valor alto en una muy buena estabilidad y respetarlo en sus especificaciones de exactitud.
Desafortunadamente, estas no son las únicas fuentes posibles de error. Vibraciones, interferencias electromagnéticas, posición de montaje del sensor, fuente de alimentación e, incluso, la carga del instrumento de evaluación pueden afectar a la exactitud de su sensor de presión. Por lo tanto, en muchos casos se recomienda la consulta individual de un especialista.
Conclusión
¿Conoce la exactitud exacta de su sensor? ¿Es tan buena como esperaba? ¿O es demasiado buena? Usted es la única persona que decide qué errores son relevantes y cuáles no. Los consultores de aplicaciones de los fabricantes explican qué características del producto son importantes para ellos y cómo se pueden implementar en su aplicación. De esta forma se garantiza que logrará sus objetivos con una entrada óptima. Nos encantará orientarle para que averigüe cuál es la exactitud que tiene actualmente y cuál es la que realmente necesita.
No dude en ponerse en contacto con nosostros para más información.
Excelente documento.
Gracias Marcelo.
Hola, gracias por visitar nuestro blog y por tus comentarios nos da mucho gusto que disfrutes nuestro contenido.