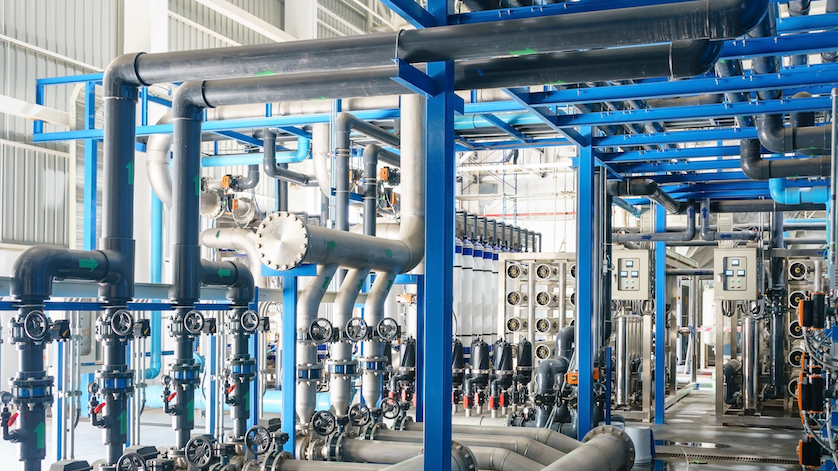
By measuring differential pressure, users are able to easily and accurately monitor filter conditions, liquid levels in closed tanks, liquid flow rates inside a pipe, and even the output torque of hydraulic motors.
There are three methods of measuring pressure. The most common type of pressure measurement is gauge pressure, with reference to atmospheric pressure. This is any pressure applied to the system on top of atmospheric pressure, also known as ambient pressure. A prime example of gauge pressure measurement is a car’s tire pressure.
Absolute pressure, with reference to a full vacuum, measures pressure independently of changes in atmospheric pressure. Absolute pressure measurement is used in applications where it is critical to monitor the peak of a vacuum, and is needed in laboratories, meteorology, aviation, and other fields.
Basics of Differential Pressure and DP Gauges

Δp = p1 – p2
Differential pressure – the third method of measuring pressure – is simply the difference between two applied pressures, often referred to as delta p (Δp). In the example, Δp = p1 – p2.
But why even use a differential pressure (DP) gauge? Why not just place a standard pressure gauge at the p1 and p2 measurement locations, and then have a technician work out the difference? Besides the extra time and effort required for manual calculations, a DP gauge is superior for several reasons:
- Sensitivity. Differential pressure gauges are designed to detect minute differences that the human eye cannot see. As an example, let’s put two standard gauges on either side of a filter. Both pointers might indicate 100 psi, but a DP gauge would be sensitive enough to pick up a difference of as low as 10″ H2O (inches water column), or 0.36 psi. A differential pressure gauge indicates only the Δp; it basically eliminates all the unnecessary “noise.”
- Range. The range of a differential pressure gauge can go as low as 0.2″ H2O for air handling systems and as high as 15,000 psi with a Bourdon tube DP gauge. Even at very low differential pressure ranges, the DP gauge must be rugged enough to withstand very high working pressures.
- Working pressure. Besides the differential pressure range, the maximum working pressure is very critical. Without knowing the working pressure, we cannot determine the correct DP gauge for the application. The working pressure in almost every DP application is significantly higher than the actual DP range.
- Options. Differential applications often require different pressure port positions, additional pressure ports, and different process connections than the typical ¼” or ½” NPT male thread used on standard gauges. For liquid level measurements, a combined top/bottom connection (total of four pressure ports) in combination with a ¼” NPT female thread can be the norm. For filter applications, in-line connections (also known as end connections) are typical, and to measure the low pressure in air handling systems, a hose barb connection is the one most often used.
There are also many options for units of measurement other than just psi, bar, and inches of water column. If measuring content in liquid level applications, users can choose among scales that read in pounds, kilograms, or gallons. In flow applications, differential pressure gauges often read in SCFM (standard cubic feet per minute), GPM (gallons per minute), m³/s (cubic meters per second), etc. And in aviation, using pitot tubes, a differential pressure gauge measures airspeed in knots or miles.
Four Applications for Differential Pressure Measurement
Differential pressure measurement goes beyond regular pressure measuring. Indeed, this type of pressure measurement is the means by which many industries monitor filter conditions, liquid level, liquid flow rate, and torque output.

Model 700.04 DP gauge
1. Filter monitoring
This is the most common application for differential pressure measurement, used in industrial oil filter applications, air filter monitoring in gas turbines, and filter monitoring – such as membrane sensing – in water/wastewater facilities. DP gauges for these industries include models 700.04, 732.25, and 732.51. To detect very low pressure in commercial and industrial HVAC systems, products in WIKA’s air2guide series, such as the A2G-10, are excellent options, as is the 716.11.
As the filter becomes clogged, the differential pressure increases. For extra convenience and performance, choose a DP gauge with an output signal, like the A2G-15, to remotely monitor the status of a filter.

Liquid level measurement in a sealed tank
2. Liquid level measurement
In an open vessel where nothing is pressurized, a simple pressure gauge is sufficient for calculating the liquid level. But in a sealed tank with liquid and gas phases, the only way to monitor that liquid level is to deduct the low-pressure side (gas or vapor) from the high-pressure side (liquid).
WIKA has about a dozen technologies for measuring tank level. The choices include the Cryo Gauge for liquid gas tanks, which can be accessorized with liquid-level and working-pressure transmitters for using the output signal in a telemetry system. A telemetry device is used to remotely monitor your customer’s tank level and to deploy a refill as needed.
3. Flow measurement

FlowPak flow meter
A primary flow element, such as an orifice plate, flow nozzle, Venturi tube, Venturi nozzle, or our high-accuracy FlowPak (FLC-HHR-FP), creates a constriction from a larger upstream diameter (point 1) to a smaller downstream diameter (point 2). This constriction in a pipe causes a pressure drop that is proportional to the square of the flow rate. Using Bernoulli’s equation, one can relate the differential pressure of the fluid with its flow velocity. Thus, the combination of a differential pressure gauge and a primary flow element creates a reliable flow meter.
4. Drill head monitoring
In hydraulic systems, a Bourdon tube-type DP gauge can be used for measuring the output torque of positive displacement motors. The gauge measures the pressure drop of the motor powering the gearbox by simultaneously measuring the pressure on the pressure and return sides of equipment during operation. By measuring the pressure drop, the DP gauge calculates the amount of torque that the hydraulic motor generates.
How to Select a Differential Pressure Gauge
Similar to selecting a standard pressure gauge, several criteria go into the selection of a DP gauge. Here are some questions to ask when choosing a differential pressure gauge:
- What differential pressure range does the application call for? This is the pressure difference that you want the scale to read.
- What is the maximum working pressure of the process? This is the maximum pressure at which the system is capable of operating for a sustained period.
- What media will the wetted parts come into contact with? The wetted parts of a regular gauge are basically just the Bourdon tube and process connection. A differential pressure gauge sometimes has two chambers; in one chamber, more parts – the movement, pointer, dial, window, and gasket – might come into contact with the media. Corrosive media might require stainless steel or a special material.
- What is the application? The choice of DP gauge often depends on whether it is used for filter monitoring, liquid level measurement, flow measurement, or drill head monitoring.
- Are there any special requirements? WIKA manufactures DP gauges for specific industries, such as NACE-compliant gauges for sour gas (hydrogen sulfide) service or gauges cleaned for oxygen service.
- What type of mounting will the gauge need? Mounting can be very specific to the industry. Furthermore, some DP gauges can be very bulky and heavy, weighing up to 30 lbs (13.6 kg). A customer can choose from different types of brackets – not just front or rear flange, but also pipe-mount brackets, Barton brackets, “H” or “C” brackets for liquid level measurement, etc.
- How about other options? WIKA’s differential pressure gauges can come with switches for automating processes, output signals for remote monitoring, and manifolds that include shut-off valves and a bypass for pressure equalizing.
The WIKA Difference for Differential Pressure Measurement
WIKA is a global leader when it comes to pressure solutions, and differential pressure measurement is no exception. What separates us from our competitors is the breadth of our products. Many of our competitors specialize in only one or two technologies. We have eight different types of DP technologies:
• Piston type
• Piston type with diaphragm
• Frictionless magnetic movement
• Bourdon tube
• Single diaphragm
• Dual diaphragm
• Capsule
• Compression spring with diaphragm
We offer all DP technologies except for bellows because of their susceptibility to pressure spikes, especially in liquid level measurement applications. A better choice would be any of the diaphragm technologies.
With 41 different models of differential pressure gauges, customers have plenty of choices, which some might find challenging to navigate. That’s why before making a purchase, it’s always a good idea to contact us first. The pressure specialists at WIKA USA can help you find the best products for your specific application and requirements.
- Model 700.04 differential pressure gauge with magnetic-piston sensing element
- Model 732.25 differential pressure gauge with membrane sensing element
- Models 732.X1 differential pressure process gauges, diaphragm element series
- Model A2G-10 differential pressure gauge for HVAC, air2guide series
- Models 716.11, 736.11 differential pressure gauge for very low DP (from 2.5 mbar)
- Model A2G-15 differential pressure gauge with output signal for HVAC
- Model FLC-HHR-FP FlowPak flow meter
Very good and informative article.