
With repeated exposure to high temperatures, a Type K thermocouple becomes less accurate. Aging is a phenomenon that results in higher-than-accurate temperature readings, while drift results in lower-than-accurate readings. While all Type K thermocouples experience aging and drift, best practices can minimize the risks and prolong thermocouple life.
Reliable, durable, and inexpensive, Type K thermocouples are commonly used in many industries. The standard mineral insulated (MI) Type K thermocouple has three metals, all of which affect its aging and drift.
In this thermocouple type, the positive conductor is made of Chromel® (a nickel and chromium alloy) and the negative conductor is made of Alumel® (an alloy of nickel, manganese, silicon and aluminum). The third metal involved is the protective sheath, which is often made of stainless steel or a similar alloy, a nickeled alloy, or a passivated nickel alloy.
The terms aging and drift are often used interchangeably when talking about how thermocouple output becomes less accurate over time as a response to temperature and movement. For the purpose of this article, aging in Type K thermocouples is a phenomenon that occurs between 600°F (316°C) and 1,200°F (649°C). Aging will result in a slight increase in the temperature reading of a sensor. Also for the purpose of this article, drift in Type K thermocouples is a phenomenon that occurs above 1,200°F (649°C) and can result in a significant decrease in the temperature reading.
With an operating temperature range of −40 to 2,300°F (−40 to 1,260°C), all Type K thermocouples will experience aging and drift over time. However, measures can be taken to reduce these effects.
The following information is based on industry findings as well as ongoing research and development at WIKA USA.
Aging and Short Range Ordering in Type K Thermocouple

Below the Curie temperature, neighboring magnetic spins align in a ferromagnet even if there is no magnetic field.
Short range ordering (SRO) is a material state where atoms are arranged regularly and predictably over only a short distance. For ferromagnetic and anti-ferromagnetic metals, SRO refers to the disordering of the electron spins from an aligned state (all pointing magnetic north) to a slightly more random orientation.This metallurgical characteristic affects Type K thermocouples regardless of wire size, manufacturer of the thermocouple wires, or manufacturer of the finished MIMS (mineral insulated metal sheathed) cable, often called a metal sheathed TI.

Above the Curie temperature, the magnetic spins are randomly aligned unless a magnetic field is applied.
The characteristic of aging is a magnetic disordering of the metal structure, which can cause small shifts in the temperature reading of the thermocouple. The nickel in the conductors is magnetic. As nickel reaches its Curie temperature[i] of 669°F (354°C), its magnetic properties begin to change and weaken, which affects the voltage differential generated by the junction of the dissimilar metals.
Short range ordering happens within a temperature range of 600–900°F (316–482°C). It can also occur, to a lesser degree, in the range of 900–1,200°F (482–649°C). This shift can be corrected by an anneal step at approximately 1,600–1,650°F (871– 899°C), but it will again be a factor as this is a characteristic of Type K wire alloys. The amount of shift decreases with multiple events that cause SRO, and the normal maximum temperature deviation is typically +5°F to +6°F.
Below is an example of a typical progression of the expected shifts in temperature reading for a Type K thermocouple with an annealed sheath.
- Start condition: The thermocouple’s temperature reading is normal as verified by comparison (in a temperature controlled bath) to a high-accuracy reference probe. The temperature reading is 700°F (371.1°C).
- This thermocouple is either put in service at exactly 700°F or put back in the same calibration bath at exactly 700°F. Due to short range ordering, the new temperature reading is 702°F (372.2°C), an increase of 2°F.
- This thermocouple experiences decreasing magnetism and is aging. When it is either put back in service (at exactly 700°F) or put back in the same calibration bath, the new temperature reading is 703.5°F (373°C), an increase of 1.5°F.
- Step 3 is repeated. The new temperature reading is 704.5°F (373.6°C), an increase of 1°F.
- Step 4 is repeated. The new temperature reading is 705°F (373.9°C), an increase of 0.5°F. After this point, any shifts in temperature reading are very small. Above 1,200°F (649°C), the shift in temperature reading will slowly “correct back” to the original calibration.
Other types of thermocouples also experience SRO and, thus, an upward shift in temperature output. In a Type J thermocouple, for example, one conductor wire is iron, which begins to age when it approaches its Curie temperature of 1,418°F (770°C).
What is Thermocouple Drift?
Drift is generally a downward shift in the temperature reading of the thermocouple and can be the result of several different phenomena. Drift will continue to decrease the temperature reading and may even result in thermocouple failure. Typically, this failure occurs at or before a decrease of 25°F offset from the original temperature.
The metallurgical phenomena involved in drift can be distinguished in:
- Surface modifications, which are related to changes in the thermoelements due to interactions between the thermoelements and the environment around the thermoelements.
- Bulk modifications, which are related to changes in the volume of the thermoelements.
Surface modifications can appear as:
- Oxidation (bare wire configurations)
- Depletion of elements from the thermoelements (bare wire/MIMS configuration)
- Contamination from the environment (bare wire/MIMS configuration)
- Interaction with the insulator (MIMS configuration)
- Interaction with the sheath (MIMS configuration)
Among the bulk modifications, the following phenomena can be observed:
- Phase transformations
- Grain growth
- Residual strain and dislocations annihilation
- Recrystallization
It is possible for thermocouple systems, especially those placed in fired heaters, to experience both aging and drift. However, it is very difficult or even impossible to predict the actual effects on thermocouple systems that experience temperature gradients as part of their normal operation.
How to Minimize Aging and Drift in a Type K Thermocouple
In many fired heaters, the tubeskin temperature is below 1,200°F (649°C) – the aging zone – while the flue gas is well above 2,000°F (1,093°C), the drift zone. Aging is predictable, whereas drift is less predictable, more damaging, and leads to system failure.
The following are some best practices regarding heaters for tubeskin thermocouple (TSTC):
- Minimize the amount of radiant/convective heat on the thermocouple. In other words, try to run the thermocouple on the coolest part of the tube. For double-fired designs, this may be half way around rather than on one side or the other.
- Balanced, shielded designs help convert radiant/convective heat to conductive heat.
- Keep as much of the TSTC in close contact with the tube as possible. This is extremely important as the tube becomes a heat sink. Adequate amounts of clips must be used to prevent gapping. Any gaps will get the tube closer to flue gas temperatures, which will put a thermocouple in the drift zone and eventually damage the sensor.
- Minimize or eliminate any off-tube routing. It is preferable to run the TSTC along the tube to an exit in line with the tube rather than having extended jumps from the tube to the wall exit perpendicular to the tube. Wraps of ceramic fiber such as Kaowool are good barriers to prevent ash-related flux problems, but wraps do not keep the thermocouple cool and will not keep a sensor out of the drift zone where there are long off-tube jumps.
- Piston-style exits are preferable to expansion coils. Bending increases the possibility of drift, and piston-style exits can minimize or eliminate this risk. It is especially important for high-movement furnaces like cokers to use piston-style exits wherever possible.
- If a piston-style exit is not possible, compensate by using small expansion coils. Since extra material acts as more surface area to absorb heat, it is important to minimize the size of the coils and to hide as much of the material in areas shaded from radiant/convective heat. Three or four small coils are often preferable to one large loop.
- Use temperature as a criterion when selecting the sheath material. Be careful when using the tube temperature for that determination if a suboptimal routing with long tube jumps is being used. Upgrading to a I600 or a Pyrocil D sheath can help minimize – but not eliminate – drift and result in longer thermocouple life.

In this illustration, the green box shows the areas that would be typically susceptible to aging. The red box shows the areas that could be susceptible to drift and, therefore, thermocouple damage.
Aging and drift occur due to the properties of the metals used in the Type K thermocouple. Currently it is not possible to make a drift-free or aging-free thermocouple. However, material scientists like Catherine Rae, PhD, and Dr. Michele Scervini are actively working on metallurgical modifications to create reduced-drift versions of both Type K and other thermocouples.
This article by Scervini goes into detail about drift, why it occurs, and temperature-activated metallurgical changes. This article (Scervini & Rae 2013), published in the Journal of Engineering for Gas Turbines and Power, discusses an improved nickel-based MIMS thermocouple for high-temperature gas turbine applications.
[i]Also called Curie point (named for Pierre Curie), this is the temperature at which certain magnetic materials undergo a sharp change in their magnetic properties. Below the Curie point, atoms that behave as tiny magnets spontaneously align themselves in certain magnetic materials. In ferromagnetic materials, the atomic magnets are oriented within each microscopic region (domain) in the same direction so that their magnetic fields reinforce each other. In antiferromagnetic materials, atomic magnets alternate in opposite directions so that their magnetic fields cancel each other. In ferrimagnetic materials, the spontaneous arrangement is a combination of both patterns, usually involving two different magnetic atoms, so that only partial reinforcement of magnetic fields occurs. Raising the temperature to the Curie point for any of the materials in these three classes entirely disrupts the various spontaneous arrangements, and only a weak kind of more general magnetic behavior, called paramagnetism, remains. (Source: britannica.com/science/Curie-point)
View our interactive refinery to learn more about WIKA product applications.
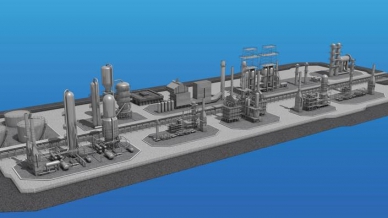
thanks for useful information